A trace to the future
10/2024: Transparency has long been the watchword of both the beverage industry and its packaging providers. Rightfully so – to root out faults with precision or to further optimise their processes, manufacturers and bottlers alike need detailed information about their bottles. To answer the call, glass packaging manufacturer Vetropack is marking their thermally hardened, lightweight reusable bottles with data matrix codes as part of a broader traceability project. Dinushika Gunasekera, Head of Smart Factory Innovations at Vetropack Austria, explains the process and the current and future uses.
Dinushika, what exactly is a data matrix code and what does it do?
At first glance, a layperson might mistake a data matrix code for a QR code. The former, however, is much more complex and requires specialised readers to decode. This is why it is typically used in industrial applications rather than for consumer-facing purposes. Each data matrix code used at Vetropack appears as a 7.5 by 7.5-millimetre square, composed of numerous small marks. The marks represent 16 characters, following the CETIE standard [1] that is commonly used in the glass industry. These characters are where it gets interesting – they convey information about the bottle, such as the exact time and location of production, down to the individual cavity of the glass forming machine used. Additionally, the code stores information about inspections the bottle underwent, for example, right before and after the thermal hardening process for our lightweight bottles. Every code is unique, allowing us to precisely identify and trace every bottle.
You mentioned the various pieces of information each data matrix code holds. How is this information actually used in practice and to what benefit?
The thorough and seamless traceability made possible by the data matrix codes offers significant benefits both to us and to the beverage producers who use our bottles. First and foremost, it is a huge plus in terms of transparency for our customers. Secondly, it plays a crucial role in precise quality control and recall management. Let me give you an example: previously, if an error occurred on one of our machines that could impact the quality of the bottles, we would have had to err on the side of caution and discard or recall a large batch of bottles produced on the machine in question. We had no way of distinguishing the bottles produced after the error occurred from the unaffected ones. The data matrix codes, however, allow us to clearly identify the bottles produced within the critical timeframe, thus significantly narrowing down the recall and saving both resources and energy.
For Vetropack, this technology enables a more analytical and data-driven approach to understanding and improving our thermally hardened, lightweight reusable bottles. The detailed data we collect via the codes allows us to gain deeper insights into how our bottles behave under various pressures and temperatures, serving as a foundation for further development and continuous optimisation.
Speaking of development – can you tell us how the data matrix code project at Vetropack started and how it progressed?
The base technology we are currently using – the laser for marking and the software for reading the codes – was developed by Bucher Emhart Glass. To deliver the results we were looking for, their technology had to be adapted to the glass forming machines as well as the thermal hardening process we are using at Vetropack. So, in 2022, we began our collaboration on the data matrix code project.
Did you encounter any challenges?
Yes, challenges are bound to crop up on such a technical project. At first, we attempted to implement a laser marking solution at the cold end of production. But marking the bottles at this temperature resulted in low-quality codes and negatively impacted the structural integrity of the glass. So, we had to go back to the drawing board and use a different method. The ideal positioning actually proved to be at the hot end: the laser marks the glass at 500 degrees Celsius and it is integrated with the forming machine to obtain production data. At this high temperature, the glass is still malleable, and the structure remains intact. The resulting data matrix code is also of a much higher quality and legibility.
We currently place the data matrix codes on the body of the bottle near the bottom. This does not interfere with monitoring filling levels, for example, as placing them on the necks of the bottles might. However, the current placement can sometimes also cause problems as some body labels are so low or large that they can cover the codes. Finding the perfect position is an ongoing development.
Apart from finding the ideal position, how else is Vetropack further developing the data matrix codes?
We will develop it further along the value chain leading to full traceability.
Thank you for this interview, Dinushika!
[1] Cf. www.cetie.org/en/
Read more
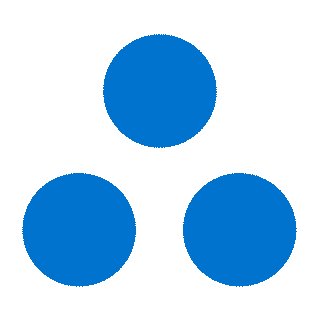