Nearing the finish line: Vetropack starts up furnaces in new plant in northern Italy
23.05.2023: After a construction period of one and a half years, glass manufacturer Vetropack has begun the process of heating up the two melting furnaces at the new Boffalora sopra Ticino plant in Italy. The furnaces will be gradually brought up to temperature and filled over the course of several days in preparation for the start of production. Upon its official inauguration in October 2023, Vetropack’s new high-tech plant will be producing up to 70 percent more glass than the previous plant, while maintaining maximum flexibility and sustainability.
Vetropack Italia S.r.l., a subsidiary of the Vetropack Group, has been producing glass packaging in Trezzano sul Naviglio in northern Italy. Now the company is relocating production to its new state-of-the-art facility in Boffalora sopra Ticino, located 25 kilometers away. Vetropack has invested more than CHF 400 million in the new production site, in order to stay ahead of rising demand in the Italian market and meet increased quality requirements. "The Italian market, with its many global brands, plays a major role in our strategy," explains Johann Reiter, CEO of the Vetropack Group. "With the start of the commissioning phase, we have reached an important milestone in Italy. Even though there are still a few steps to go before production starts – we are approaching the finish line."
Using energy with precision
Prior to heat-up, Vetropack conducted a "cold" acceptance inspection of the new furnaces in Boffalora, both outside and inside. The subsequent 24-hour test, also carried out "cold", confirmed that the furnace equipment is functioning optimally. On May 22, the first furnace was fired up, with the second furnace following a few weeks later. Initially, external burners are firing the furnaces. This process takes a total of 14 days: "The furnaces must be heated up from room temperature to 1550 degrees Celsius in a precise and controlled manner. We follow a previously calculated heating curve to prevent the furnaces from suffering any damage," explains Christoph Burgermeister, project manager at Vetropack. "In addition, the refractory material expands as a result of the heating, so we have to continuously adjust the pressure pins in the steel structure during this step of the process."
Once the furnaces have reached an internal temperature of approximately 1050 degrees Celsius, the furnace burners are activated to raise the temperature to 1550 degrees Celsius. Filling begins with waste glass cullet, which not only saves valuable resources but can also be melted down with less energy input than raw material. After two to three days, the cullet is supplemented by a mixture of primary raw materials and finally heated for about 24 hours. Thereafter, the molten glass passes via the forehearth into the feeders and through the working end, then is cut into glass gobs and fed in sequence to the automatic glass container forming machines. Depending on the progress of the commissioning, Boffalora's schedule foresees the start-up of the forming machines sequentially and closely together.
Flexible and sustainable production
According to Vetropack, the new plant will not only offer up to a 70 percent increase in production capacity compared to the Trezzano plant. The smart technologies in which the Swiss glass manufacturer is investing for the Boffalora brownfield project will also enable greater production flexibility, for example for so-called semi-specials – containers that differ from the norm, in smaller batches. In addition, the site is geared towards a significantly more resource-efficient and sustainable production, with the water used for production and exhaust heat from the melting furnaces recycled as far as possible through recirculation systems, and emissions greatly reduced through the latest filter systems.
With the new site opening, the previous plant in Trezzano sul Naviglio will be closed down. Boffalora sopra Ticino will remain as the sole Vetropack site in Italy. However, the 301 employees will not have to fear for their jobs, as all staff members of the previous site have been offered a transfer. With the significant increase in productivity, the current workforce, which already includes employees hired in the recent past to secure the necessary training, will continue to grow to meet production needs.
Downloads
- PI_E_Vetropack_Heat-up_Boffalora.pdf (pdf)
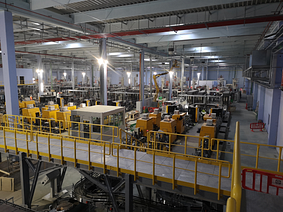
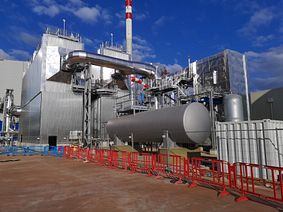
About Vetropack Group
At Vetropack, we enable people to enjoy food and beverages as safely as possible by providing solutions that combine optimum elegance with maximum responsibility. We view glass as the most sustainable packaging solution – and the perfect material to ensure that food is packaged safely. Our holistic Service plus+ approach helps our customers to optimise their value chains and guarantee consumers' safety. Close, long-lasting relationships are the hallmarks of our collaboration with partners. Guided by our understanding of environmental responsibility and cost efficiency, we aim to minimise our carbon footprint throughout the supply chain, and we are committed to recycling as the key to optimising product life-cycles.
Vetropack Group is one of Europe's leading manufacturers of glass packaging for the food and beverage industry with around 4,000 employees and net revenues of CHF 899.4 million in 2022. Vetropack has state-of-the-art production facilities as well as sales and distribution offices in Switzerland, Austria, the Czech Republic, Croatia, Slovakia, Ukraine, Italy, the Republic of Moldova and Romania.