A day with Riccardo Riso
As Continuous Improvement Manager, Riccardo Riso identifies opportunities for optimising our production and works together with his colleagues on implementing best practices throughout Vetropack Group. For example in Chișinău, where we shadow him for a day.
«Based in Trezzano, I spend most of my week across our plants. This week, I am in Chișinău, together with my colleagues from the Technical Performance Team. We are working together with the local team to integrate the latest plant into Vetropack Group from a technical standpoint. We are looking at where exactly we can benefit the most from implementing group standards and best practices.»
To do this, we need to first understand the situation and processes on site. So we walk through the production area and the workshops. We also observe, discuss and collaborate with everyone involved in the production processes, as well as those involved in safety, quality, the supply chain and controlling.
That is why, today, we are looking at the current production set-up and its key figures: What is safety like in the plant? What do our customers really value about our products? How are our main productivity indicators going? What about the skills, the mindset and the competencies of the colleagues in the plant? What best practices, if adopted, could help the plant team to unleash its potential and reach the next performance level?
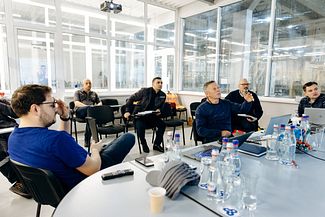
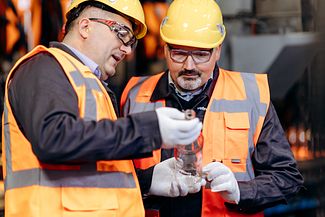
Together, we take a closer look at a job change at the hot end: How can we make the work easier? Where are the bottlenecks in the process? What can we do to eliminate waste? How can we improve ergonomics, quality and speed? Our focus is on optimising the value we can bring to the customer, to increase their satisfaction and reach our business goals.
So we aim to continuously improve our products, services and processes. Continuous improvement is not about quick fixes to problems but understanding the root causes and addressing them in close collaboration with all the colleagues involved at plant, business unit and group level. This ensures we learn and get better at problem solving together.
In Chișinău, we will continue work on this in the coming months, supporting the plant in terms of job changes and improving energy efficiency. It is also a case reassessing the organisation and building a structure that can support the performance level required.
Besides this, I will be working closely with other sites in the coming months as part of the “Performance Improvement Programme”.
Colleagues across VPA, whose two plants are the first involved in the programme, have already highlighted almost one hundred improvement ideas. These include technical solutions to reduce the weight of our glass containers. Or different ways to maintain moulds with a view to reducing work and wear. Or even solutions to reduce waste and improve our materials efficiency, and many others too.
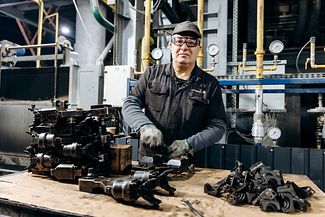
We are now defining and prioritising all these potential measures based on our business objectives: Where do we expect the greatest financial benefit in relation to the effort? What is our roadmap to achieve them? In this endeavour, I work very closely with controlling, who help us set priorities, through financials indicators, and who assess the financial benefits of our measures.
As project manager, I provide a clear structure and tools on how we can plan and implement the projects and present and evaluate their results. One thing I have learned in my many years of work as Continuous Improvement Manager in the glass industry is that people are the most important factor in the success of an organisation.
That is why I also see myself also as bridge builder: connecting people, processes and technology – and this is where my training in engineering and social psychology can help. It is never just about introducing new processes or tools. Improvement only occurs when it is properly discussed, communicated, and adopted – and finally embedded in the corporate culture and in people’s mindset.
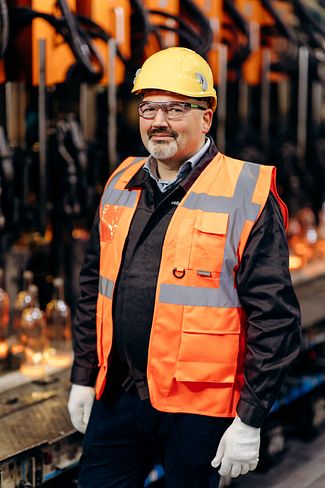